Hoe worden onderdelen met hoge precisie bewerkt?
2023-09-22
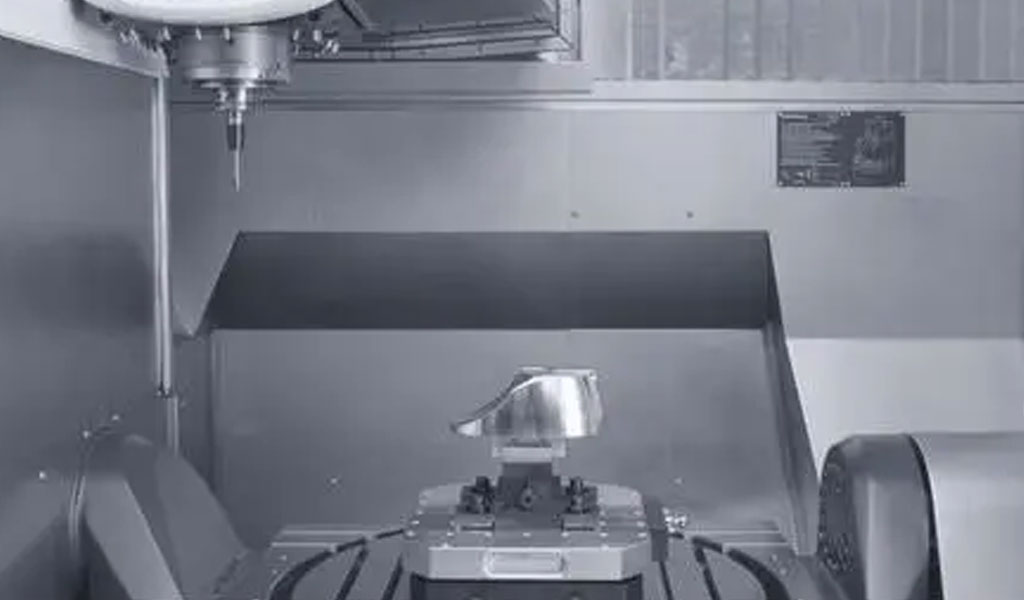
Precisiebewerking begrijpen
Precisiebewerking is een hoeksteen van de moderne productie en is verantwoordelijk voor de productie van ingewikkelde en nauwkeurige componenten die in een breed scala van industrieën worden gebruikt. Laten we, om de betekenis ervan volledig te begrijpen, de kernconcepten van precisiebewerking verkennen, de cruciale rol ervan in verschillende sectoren en de historische reis die heeft geleid tot de huidige staat van uitmuntendheid.A. Wat is precisiebewerking?
Precisiebewerking verwijst naar een reeks productieprocessen waarbij materiaal met een hoge mate van nauwkeurigheid en controle uit een werkstuk wordt verwijderd, wat resulteert in fijn vervaardigde componenten met nauwe toleranties. Dit proces transformeert grondstoffen, zoals metalen, kunststoffen of keramiek, in precieze onderdelen die aan strenge specificaties voldoen. De belangrijkste kenmerken van precisiebewerking zijn onder meer:- Nauwkeurigheid: Precisiebewerking zorgt ervoor dat het eindproduct precies voldoet aan het beoogde ontwerp, met minimale afwijkingen.
- Strakke toleranties: Het maakt de productie mogelijk van onderdelen met extreem nauwe toleranties, wat betekent dat de afgewerkte componenten nauw aansluiten bij de gespecificeerde afmetingen.
- Superieure oppervlakteafwerking: Precisiebewerking zorgt voor uitzonderlijke oppervlakteafwerkingen, waardoor vaak geen extra afwerkingsprocessen nodig zijn.
- Complexe geometrieën: Het kan ingewikkelde vormen, contouren en kenmerken creëren, waardoor het onmisbaar wordt bij de productie van componenten met complexe ontwerpen.
- Herhaalbaarheid: Precisie bewerkingsproces:es zijn zeer herhaalbaar, waardoor een consistente kwaliteit voor meerdere onderdelen wordt gegarandeerd.
- Veelzijdigheid: Het kan worden toegepast op een breed scala aan materialen, waardoor het geschikt is voor diverse industrieën.
B. Belang van precisiebewerking
Precisiebewerking is van enorme betekenis in verschillende cruciale industrieën en heeft een impact op verschillende aspecten van ons dagelijks leven. Hier zijn enkele overtuigende redenen voor het belang ervan:- Luchtvaartindustrie: In de lucht- en ruimtevaartsector is precisiebewerking onmisbaar voor het vervaardigen van componenten die bestand zijn tegen extreme omstandigheden. Vliegtuigmotoren, landing versnellingen structurele elementen zijn voor veiligheid en prestaties afhankelijk van nauwkeurig bewerkte onderdelen.
- Medical Devices: Medische apparaten zoals chirurgische instrumenten, protheses en implanteerbare apparaten vereisen precisiebewerking voor biocompatibiliteit, nauwkeurigheid en patiëntveiligheid.
- Automobielsector: Nauwkeurig bewerkte onderdelen zijn essentieel voor de auto-industrie om de betrouwbaarheid en efficiëntie van voertuigen te garanderen. Componenten zoals motoronderdelen, transmissiesystemen en remmechanismen zijn afhankelijk van nauwkeurige bewerking.
- Elektronica en halfgeleiders: Precisiebewerking is cruciaal bij de productie van micro-elektronische componenten en halfgeleiderapparaten, waarbij minuscule toleranties absoluut noodzakelijk zijn voor functionaliteit.
- Energiesector: De energie-industrie vertrouwt op precisiebewerking voor de productie van cruciale onderdelen die worden gebruikt bij de energieopwekking, waaronder turbines, generatoren en transmissiecomponenten.
- Gereedschap en matrijzenbouw: Precisiebewerking is cruciaal bij de productie van gereedschappen en matrijzen, die op hun beurt worden gebruikt om talloze andere producten te maken.
- Consumer Electronics: De productie van smartphones, laptops en andere consumentenelektronica profiteert van precisiebewerking om strakke ontwerpen en optimale functionaliteit te garanderen.
- Research and Development: Onderzoekers en wetenschappers zijn afhankelijk van nauwkeurig bewerkte componenten voor experimenten, prototypes en laboratoriumapparatuur.
C. Historisch perspectief
De reis van precisiebewerking gaat terug tot oude beschavingen, waar bekwame ambachtslieden rudimentaire gereedschappen gebruikten om materialen te vormen. De in die tijd bereikte precisie was echter beperkt vergeleken met hedendaagse normen.- Vroege precisiebewerking: De industriële revolutie van de 18e en 19e eeuw markeerde een cruciale periode in de ontwikkeling van precisiebewerking. De uitvinding van werktuigmachines, zoals draaibanken en freesmachines, bracht een revolutie teweeg in de productie door een grotere nauwkeurigheid en consistentie mogelijk te maken.
- De Tweede Wereldoorlog: Precisiebewerking speelde een cruciale rol in de Tweede Wereldoorlog, omdat het essentieel was voor het produceren van militair materieel met de vereiste precisie en uniformiteit. Dit tijdperk was getuige van vooruitgang in bewerkingstechnieken en de opkomst van nieuwe materialen.
- Naoorlogse vooruitgang: In de naoorlogse periode was sprake van een sterke toename van technologische innovaties, waaronder het gebruik van CNC-machines (computer numerieke besturing). CNC-bewerking maakte geautomatiseerde en zeer nauwkeurige bewerkingen mogelijk, wat een nieuw productietijdperk inluidde.
- Het digitale tijdperk: De integratie van computers en software in bewerkingsprocessen heeft de precisiebewerking verder verbeterd. Moderne CNC-machines kunnen complexe bewerkingen met een ongeëvenaarde nauwkeurigheid uitvoeren, waardoor ze onmisbaar zijn in het huidige productielandschap.
Materialen en hun betekenis
Materialen vormen de basis van precisiebewerking en de selectie van het juiste materiaal speelt een cruciale rol bij de productie van onderdelen met hoge precisie. In dit gedeelte gaan we dieper in op het belang van het selecteren van de juiste materialen, begrijpen we het belang van materiaaleigenschappen en onderzoeken we de verschillende factoren die de bewerkbaarheid beïnvloeden.A. Selectie van materialen
De materiaalkeuze bij precisiebewerking is een cruciale beslissing die rechtstreeks van invloed is op de prestaties, duurzaamheid en functionaliteit van het eindproduct. Fabrikanten moeten bij het selecteren van materialen rekening houden met verschillende factoren:- Materiële geschiktheid: Het materiaal moet geschikt zijn voor de beoogde toepassing. Verschillende industrieën en toepassingen stellen verschillende eisen, zoals temperatuurbestendigheid, corrosieweerstand en elektrische geleidbaarheid.
- Mechanische eigenschappen: Mechanische eigenschappen zoals treksterkte, hardheid en ductiliteit zijn cruciaal. In de lucht- en ruimtevaart hebben materialen met een hoge treksterkte bijvoorbeeld de voorkeur voor structurele componenten.
- Thermische eigenschappen: Sommige toepassingen vereisen materialen met uitstekende thermische geleidbaarheid of weerstand tegen hoge temperaturen. Dit is vooral belangrijk in sectoren als energieopwekking en elektronica.
- Corrosiebestendigheid: In omgevingen waar corrosie een probleem is, wordt de voorkeur gegeven aan materialen met een hoge weerstand tegen corrosie, zoals roestvrij staal of titanium.
- Gewichtsoverwegingen: Industrieën als de automobiel- en ruimtevaartsector geven vaak prioriteit aan lichtgewicht materialen zoals aluminium of koolstofvezelcomposieten om het brandstofverbruik te verminderen en de prestaties te verbeteren.
- Kostenbeperkingen: Kosten zijn een belangrijke factor bij de materiaalkeuze. Hoogwaardige materialen kunnen duur zijn, dus fabrikanten moeten een evenwicht vinden tussen prestaties en kosteneffectiviteit.
- Regulatory Compliance: In industrieën zoals de gezondheidszorg moeten materialen voldoen aan strenge wettelijke normen voor biocompatibiliteit en veiligheid.
- Beschikbaarheid: De beschikbaarheid van materialen en hun bronnen hebben ook invloed op de selectie. Sommige gespecialiseerde legeringen of composieten zijn mogelijk beperkt verkrijgbaar.
B. Materiaaleigenschappen
Het begrijpen van de eigenschappen van materialen is cruciaal voor precisiebewerking. Hier zijn enkele belangrijke materiaaleigenschappen en hun betekenis:- Treksterkte: Treksterkte meet het vermogen van een materiaal om een trekkracht te weerstaan zonder te breken. Het is essentieel voor structurele componenten en onderdelen die worden blootgesteld aan mechanische spanning.
- Hardheid: Hardheid geeft de weerstand van een materiaal tegen vervorming en slijtage aan. Harde materialen zijn geschikt voor snijgereedschappen, terwijl zachtere materialen voor bepaalde toepassingen, zoals afdichtingen, de voorkeur kunnen hebben.
- buigzaamheid: Ductiliteit verwijst naar het vermogen van een materiaal om te vervormen zonder te breken wanneer het wordt blootgesteld aan trekspanning. Ductiele materialen zijn gemakkelijker te vormen, maar zijn mogelijk niet geschikt voor toepassingen die stijfheid vereisen.
- Warmtegeleiding: Materialen met een hoge thermische geleidbaarheid voeren de warmte efficiënt af. Deze eigenschap is van vitaal belang in toepassingen waarbij temperatuurregeling van cruciaal belang is.
- Elektrische geleiding: Elektrische geleidbaarheid is essentieel in elektronica en elektrische componenten, waar materialen de stroom van elektriciteit moeten vergemakkelijken.
- Magnetische eigenschappen: Magnetische eigenschappen zijn van groot belang in industrieën als elektromagnetisme en elektronica, waar materialen ferromagnetisch of niet-magnetisch moeten zijn.
- Chemische weerstand: Materialen moeten bestand zijn tegen chemische corrosie in omgevingen waar ze worden blootgesteld aan zuren, basen of andere corrosieve stoffen.
C. Bewerkbaarheidsfactoren
Bewerkbaarheid verwijst naar het gemak waarmee een materiaal kan worden bewerkt, gesneden of gevormd. Het wordt beïnvloed door verschillende factoren, waaronder:- Materiële hardheid: Zachtere materialen zijn over het algemeen gemakkelijker te bewerken, terwijl voor hardere materialen mogelijk gespecialiseerd gereedschap en technieken nodig zijn.
- Chipvorming: De vorming en afvoer van spanen tijdens de bewerking beïnvloeden de efficiëntie en de oppervlakteafwerking van het proces.
- Slijtage van gereedschap: Verschillende materialen kunnen verschillende mate van gereedschapsslijtage veroorzaken, wat een invloed heeft op de bewerkingssnelheid en -kosten.
- Koelvloeistof en smering: De juiste koelvloeistof en smering zijn essentieel om wrijving, hitte en gereedschapslijtage tijdens het bewerken te verminderen.
- snijsnelheid: De snelheid waarmee het snijgereedschap door het materiaal beweegt, heeft invloed op zowel de productiviteit als de kwaliteit van het bewerkte oppervlak.
- Gereedschapsmateriaal: De keuze van het snijgereedschapsmateriaal, zoals hardmetaal of snelstaal, hangt af van het materiaal dat wordt bewerkt.
- Snijparameters:: Het aanpassen van snijparameters zoals voedingssnelheid en snedediepte kan het bewerkingsproces voor specifieke materialen optimaliseren.
Werktuigmachines voor precisiebewerking
Werktuigmachines vormen het hart van precisiebewerking en maken de transformatie van grondstoffen in onderdelen met hoge precisie mogelijk. In dit gedeelte onderzoeken we vier belangrijke soorten werktuigmachines die worden gebruikt bij precisiebewerking: CNC-bewerkingscentra, draaimachines, slijpmachines en EDM (Electrical Discharge Machining). Elk van deze machines speelt een unieke rol bij de productie van precieze componenten.A. CNC-bewerkingscentra
CNC-bewerkingscentra (Computer Numerical Control) zijn veelzijdig en worden veel gebruikt bij precisiebewerking. Het zijn geautomatiseerde systemen die de beweging van snijgereedschappen en werkstukken met uitzonderlijke precisie controleren. Hier vindt u een overzicht van CNC-bewerkingscentra en hun betekenis:- Veelzijdigheid: CNC-bewerkingscentra kunnen verschillende bewerkingen uitvoeren, waaronder frezen, boren en tappen. Deze veelzijdigheid maakt de productie van complexe onderdelen met meerdere functies mogelijk.
- Hoge precisie: De computergestuurde besturing van CNC-machines zorgt voor een nauwkeurige positionering van het gereedschap en consistente resultaten, waardoor ze ideaal zijn voor onderdelen met nauwe toleranties.
- Automatisering: CNC-bewerkingscentra kunnen continu werken, met minimale menselijke tussenkomst. Deze automatisering verhoogt de efficiëntie en verkleint de kans op fouten.
- Complexe geometrieën: Ze blinken uit in het bewerken van ingewikkelde vormen en contouren, waardoor ze geschikt zijn voor industrieën zoals de lucht- en ruimtevaart, waar complexe componenten gebruikelijk zijn.
- Herhaalbare resultaten: CNC-machines bieden uitstekende herhaalbaarheid, waardoor elk geproduceerd onderdeel overeenkomt met de exacte specificaties van het ontwerp.
- Kortere insteltijden: CNC-bewerkingscentra kunnen worden geprogrammeerd om snel tussen verschillende taken te schakelen, waardoor de insteltijden worden geminimaliseerd en de productie-efficiëntie wordt verhoogd.
B. Draaimachines
Draaimachines worden gebruikt om cilindrische onderdelen te maken door een werkstuk te roteren terwijl een snijgereedschap materiaal van het buitenoppervlak verwijdert. Ze zijn essentieel voor de productie schachts, pinnen en andere componenten met rotatiesymmetrie. Belangrijke punten over draaimachines zijn onder meer:- Cilindrische onderdelen: Draaimachines zijn gespecialiseerd in het produceren van cilindrische of buisvormige onderdelen, inclusief onderdelen met schroefdraad of ingewikkelde groeven.
- Hoge snelheden: Ze werken op hoge snelheden, waardoor ze geschikt zijn voor onderdelen die een gladde en nauwkeurige afwerking vereisen.
- Bediening met één as: De meeste draaimachines zijn enkelassig en richten zich op het vormgeven van het buitenoppervlak van het werkstuk.
- Efficiënt voor massaproductie: Draaien is zeer efficiënt voor massaproductie van onderdelen met minimaal materiaalverlies.
- Draaibankmachines: Handmatige en CNC-gestuurde draaibanken zijn veelgebruikte draaimachines en bieden een scala aan mogelijkheden.
C. Slijpmachines
Slijpmachines zijn ontworpen voor het nauwkeurig afwerken van oppervlakken en het vormen van harde of schurende materialen. Ze zijn cruciaal voor het bereiken van extreem nauwe toleranties en superieure oppervlakteafwerkingen. Dit is waarom slijpmachines belangrijk zijn:- Precisie op micronniveau: Slijpmachines kunnen precisie op micronniveau bereiken, waardoor ze essentieel zijn voor toepassingen die het hoogste nauwkeurigheidsniveau vereisen.
- Materiaal verwijderen: Ze verwijderen materiaal door schuren, waardoor oneffenheden in het oppervlak kunnen worden gecorrigeerd en een uitzonderlijke gladheid wordt bereikt.
- Gereedschap- en freesslijpen: Naast het vlakslijpen zijn er gespecialiseerde slijpmachines voor het slijpen van snijgereedschappen en het maken van nauwkeurige profielen.
- Verscheidenheid aan maalmethoden: Verschillende soorten slijpmachines, waaronder vlakslijpmachines, cilindrische slijpmachines en centerloze slijpmachines, komen tegemoet aan verschillende bewerkingsbehoeften.
- Geharde materialen: Slijpen is bijzonder geschikt voor geharde materialen zoals gereedschapsstaal en keramiek, waarbij traditionele bewerkingsmethoden mogelijk niet effectief zijn.
D. EDM (bewerking met elektrische ontlading)
EDM, of Electrical Discharge Machining, is een niet-traditioneel bewerkingsproces waarbij elektrische ontladingen worden gebruikt om materialen te vormen. Het is ideaal voor het maken van ingewikkelde en delicate onderdelen waar traditionele snijgereedschappen schade kunnen veroorzaken. De belangrijkste aspecten van EDM zijn onder meer:- Geen fysiek contact: Bij EDM is er geen direct fysiek contact tussen het gereedschap en het werkstuk, waardoor het risico op gereedschapsslijtage en schade aan kwetsbare materialen wordt geminimaliseerd.
- Hoge precisie: Het kan een hoge precisie en oppervlaktekwaliteit bereiken, zelfs met uitzonderlijk harde materialen.
- Draadvonken en zinkloodvonken: Er zijn twee hoofdtypen EDM-machines: draad snijden EDM, waarbij gebruik wordt gemaakt van een draadelektrode, en zinklood-EDM, waarbij gebruik wordt gemaakt van een gevormde elektrode.
- Complexe vormen: EDM kan complexe vormen produceren, zoals matrijzen en mallen, met ingewikkelde details en fijne kenmerken.
- Door hitte beïnvloede zone: Omdat EDM geen warmte genereert aan het werkstuk, is het geschikt voor warmtegevoelige materialen zoals ruimtevaartlegeringen.
- Langzaam proces: EDM is relatief langzaam in vergelijking met andere bewerkingsmethoden, waardoor het het meest geschikt is voor kleine hoeveelheden en uiterst nauwkeurige klussen.
Snijgereedschappen en gereedschappen
Snijgereedschappen lopen voorop bij precisiebewerking en dienen als instrumenten die grondstoffen vormen en transformeren in onderdelen met hoge precisie. In dit gedeelte onderzoeken we de verschillende soorten snijgereedschappen, het belang van gereedschapscoatings en de factoren die de standtijd en slijtage beïnvloeden.A. Soorten snijgereedschappen
Precisiebewerking is afhankelijk van een breed scala aan snijgereedschappen, elk ontworpen voor specifieke taken en materialen. De keuze van het snijgereedschap heeft grote invloed op de efficiëntie en nauwkeurigheid van het bewerkingsproces. Hier zijn enkele veel voorkomende soorten snijgereedschappen:- Einde Mills: Vingerfrezen zijn veelzijdige gereedschappen die worden gebruikt voor freesbewerkingen. Ze hebben meerdere snijkanten en kunnen op verschillende manieren materiaal van het werkstuk verwijderen, waaronder vlakken, contouren en gleufsteken.
- Boren: Boren zijn ontworpen voor het maken van gaten in werkstukken. Ze zijn er in verschillende vormen, waaronder spiraalboren, middenboren en wisselplaatboren.
- Wisselplaten: Deze worden in draaimachines gebruikt om cilindrische onderdelen te vormen. Draaiwisselplaten zijn verkrijgbaar in verschillende vormen en materialen voor verschillende toepassingen.
- Frezen: Frezen zijn er in verschillende vormen, zoals vlakfrezen, kogelmolens en gleuffrezen, en worden in freesmachines gebruikt om verschillende kenmerken op het werkstuk te creëren.
- ruimers: Ruimers worden gebruikt voor het afwerken en op maat maken van eerder geboorde gaten tot precieze afmetingen. Ze zorgen voor gladde en nauwkeurige gatoppervlakken.
- Kranen en matrijzen: Deze snijgereedschappen worden gebruikt voor draadsnijbewerkingen. Kranen creëren interne schroefdraad, terwijl matrijzen externe schroefdraad creëren.
- Slijpstenen: Slijpschijven zijn schuurmiddelen die worden gebruikt voor het nauwkeurig slijpen van oppervlakken. Ze zijn verkrijgbaar in verschillende schuurmaterialen en korrelgroftes.
- Aansnijdt: Broches zijn gespecialiseerde gereedschappen die worden gebruikt voor het snijden van interne en externe vormen en profielen, zoals spiebanen en spiebanen.
- Verzinkboren en verzinkboren: Deze gereedschappen worden gebruikt om uitsparingen of afschuiningen rond gaten te maken bevestigers.
- Saaie bars: Kotterbaren worden gebruikt bij kotterbewerkingen om bestaande gaten nauwkeurig te vergroten.
B. Gereedschapscoatings
Gereedschapscoatings zijn dunne lagen materiaal die op snijgereedschappen worden aangebracht om de prestaties en duurzaamheid ervan te verbeteren. Deze coatings bieden verschillende voordelen:- Minder wrijving: Coatings zoals titaniumnitride (TiN) en titaniumcarbonitride (TiCN) verminderen de wrijving tussen gereedschap en werkstuk, wat leidt tot soepeler snijden en een langere standtijd.
- Verbeterde hardheid: Coatings verhogen de hardheid van het oppervlak van het gereedschap, waardoor het beter bestand is tegen slijtage en de standtijd wordt verlengd.
- Verbeterde hittebestendigheid: Coatings zijn bestand tegen hoge temperaturen die tijdens de bewerking worden gegenereerd, waardoor hittegerelateerde gereedschapsslijtage wordt verminderd en de snijsnelheden worden verhoogd.
- Eigenschappen tegen opbouw: Sommige coatings hebben anti-hechteigenschappen, waardoor de ophoping van materiaal op de snijkanten van het gereedschap wordt voorkomen.
- Verhoogde gladheid: Gecoate gereedschappen hebben een verbeterde smering, waardoor er minder overmatig koelmiddel nodig is en de spaanafvoer wordt verbeterd.
C. Levensduur en slijtage van het gereedschap
Inzicht in de standtijd en slijtage van gereedschap is cruciaal voor het optimaliseren van bewerkingsprocessen en het minimaliseren van de productiekosten. De levensduur van het gereedschap verwijst naar de tijd dat een snijgereedschap effectief blijft voordat het moet worden vervangen of gereviseerd. Verschillende factoren beïnvloeden de standtijd en slijtage:- snijsnelheid: Hogere snijsnelheden kunnen leiden tot verhoogde gereedschapsslijtage als gevolg van hogere temperaturen die tijdens de bewerking worden gegenereerd. Een juiste selectie van snijsnelheden is essentieel om de standtijd en productiviteit in evenwicht te brengen.
- Voedingssnelheid: De snelheid waarmee het snijgereedschap in het werkstuk beweegt, heeft invloed op de slijtage van het gereedschap. Hoge voedingen kunnen de slijtage versnellen, terwijl lagere voedingen de standtijd kunnen verlengen.
- Diepte van de snede: De snedediepte beïnvloedt de hoeveelheid materiaal die per passage wordt verwijderd. Diepere sneden kunnen de slijtage van het gereedschap vergroten, dus het optimaliseren van de diepte is van cruciaal belang.
- Materiële hardheid: Het snijden van harde materialen kan de slijtage van het gereedschap versnellen. Gespecialiseerde gereedschappen en coatings worden gebruikt voor het effectief bewerken van harde materialen.
- Koelvloeistof en smering: Een goede koelvloeistof en smering helpen de warmte af te voeren en de wrijving te verminderen, waardoor de levensduur van het gereedschap wordt verlengd.
- Gereedschapsmateriaal: Het materiaal waaruit het snijgereedschap is gemaakt, beïnvloedt de slijtvastheid. Materialen als hardmetaal en keramiek bieden een uitstekende slijtvastheid.
- Gereedschapsgeometrie: De geometrie van het snijgereedschap, inclusief spaanhoek, ontlastingshoek en spaanbrekerontwerp, speelt een belangrijke rol in slijtagepatronen.
- Werkstuk materiaal: Het type materiaal dat wordt bewerkt, heeft invloed op de slijtage van het gereedschap. Schurende materialen kunnen leiden tot snellere gereedschapsslijtage.
Precisiebewerkingsprocessen
Precisiebewerkingsprocessen zijn de methoden waarmee grondstoffen worden omgezet in onderdelen met hoge precisie, met nauwe toleranties en uitzonderlijke oppervlakteafwerkingen. In dit gedeelte onderzoeken we vijf belangrijke precisiebewerkingsprocessen: draaien, frezen, boren, slijpen en elektrische ontladingsbewerking (EDM). Elk van deze processen dient een uniek doel en wordt toegepast op basis van de specifieke vereisten van het werkstuk.A. Draaien
Draaien is een bewerkingsproces dat voornamelijk wordt gebruikt voor het vormen van cilindrische onderdelen. Het gaat om het roteren van een werkstuk terwijl een enkelpunts snijgereedschap materiaal van het buitenoppervlak verwijdert. Dit zijn de belangrijkste aspecten van draaien:- Cilindrische onderdelen: Draaien is ideaal voor het produceren van cilindrische componenten zoals assen, pennen en hulzen.
- Rotatiesymmetrie: Het is zeer geschikt voor onderdelen die rotatiesymmetrie vereisen, omdat het werkstuk op een draaibank draait terwijl het snijgereedschap het vormt.
- Diverse operaties: Draaien kan verschillende bewerkingen uitvoeren, waaronder vlakdraaien, draaien (de diameter verkleinen), conisch draaien en draadsnijden.
- Eénpuntssnijden: Eén enkel snijgereedschap verwijdert materiaal in een continue beweging, wat resulteert in een efficiënte materiaalverwijdering.
- Draaibankmachines: Zowel handmatige als CNC-gestuurde draaibanken worden veel gebruikt voor draaibewerkingen.
B. Frezen
Frezen is een veelzijdig precisiebewerkingsproces waarbij gebruik wordt gemaakt van meerpuntssnijgereedschappen om materiaal van een werkstuk te verwijderen. Het is zeer geschikt voor het creëren van een breed scala aan vormen en functies. De belangrijkste aspecten van frezen zijn onder meer:- Veelzijdigheid: Frezen kan vlakke oppervlakken, sleuven, kamers en complexe contouren produceren. Het wordt gebruikt voor zowel 2D- als 3D-bewerkingen.
- Meerpuntssnijden: Meerdere snijkanten op het gereedschap werken tegelijkertijd samen met het werkstuk, waardoor een efficiënte materiaalverwijdering mogelijk is.
- Soorten frezen: Frezen kan worden uitgevoerd met behulp van verschillende soorten frezen, waaronder vingerfrezen, vlakfrezen en kogelmolens.
- CNC-bewerkingscentra: CNC-gestuurde freesmachines bieden nauwkeurige controle over de gereedschapsbeweging en worden veel gebruikt in de moderne verspaning.
- Hoge snelheden: Het frezen kan met hoge snelheden worden uitgevoerd, waardoor een efficiënte productie mogelijk is.
C. Boren
Boren is een precisiebewerkingsproces dat wordt gebruikt om gaten in werkstukken te maken. Het is een fundamentele operatie in verschillende industrieën. De belangrijkste aspecten van boren zijn onder meer:- Gat creatie: Boormachines gebruiken gespecialiseerd gereedschap, boren genaamd, om materiaal te verwijderen en gaten met een specifieke diameter te maken.
- Soorten boren: Er zijn verschillende soorten boren beschikbaar, waaronder spiraalboren, centrumboren en wisselplaatboren, elk ontworpen voor specifieke toepassingen.
- Nauwkeurigheid: Nauwkeurige positionering en uitlijning zijn essentieel bij het boren om ervoor te zorgen dat gaten nauwkeurig worden gemaakt.
- Snelheid en voedingssnelheid: Boorparameters zoals rotatiesnelheid en voedingssnelheid zijn van cruciaal belang voor het bereiken van de gewenste gatafmetingen.
- Koelvloeistof en smering: De juiste koelvloeistof en smering worden gebruikt om de warmte af te voeren en de wrijving tijdens het boren te verminderen.
D. Slijpen
Slijpen is een nauwkeurig bewerkingsproces waarbij gebruik wordt gemaakt van schuurwielen om materiaal te verwijderen en extreem nauwe toleranties en oppervlakteafwerkingen te bereiken. De belangrijkste aspecten van slijpen zijn onder meer:- Uitzonderlijke precisie: Slijpen kan precisie op micronniveau bereiken, waardoor het ideaal is voor toepassingen die de hoogste nauwkeurigheid vereisen.
- Oppervlaktebehandeling: Het produceert superieure oppervlakteafwerkingen, waardoor er vaak geen extra afwerkingsprocessen meer nodig zijn.
- Materialen: Slijpen is geschikt voor harde en schurende materialen, waaronder gehard staal, keramiek en carbiden.
- Verscheidenheid aan maalmethoden: Verschillende soorten slijpmachines, zoals vlakslijpmachines, cilindrische slijpmachines en centerloze slijpmachines, komen tegemoet aan verschillende bewerkingsbehoeften.
- Koelmiddel: De juiste koelvloeistof is essentieel bij het slijpen om oververhitting te voorkomen en de integriteit van de schijf te behouden.
E. Machinale bewerking door elektrische ontlading (EDM)
EDM, of Electrical Discharge Machining, is een niet-traditioneel precisiebewerkingsproces waarbij gebruik wordt gemaakt van elektrische ontladingen om materiaal te verwijderen. Het is bijzonder geschikt voor het bewerken van complexe en ingewikkelde vormen, evenals harde en hittebestendige materialen. De belangrijkste aspecten van EDM zijn onder meer:- Contactloze bewerking: Bij EDM is er geen direct contact tussen het gereedschap en het werkstuk, waardoor het risico op gereedschapsslijtage en schade wordt verminderd.
- Hoge precisie: EDM kan een hoge nauwkeurigheid bereiken, waardoor het geschikt is voor toepassingen waarbij nauwe toleranties essentieel zijn.
- Complexe vormen: Het blinkt uit in het bewerken van complexe vormen, matrijzen, mallen en componenten met fijne details.
- Draadvonken en zinkloodvonken: Er zijn twee hoofdtypen EDM-machines: draadvonken, waarbij gebruik wordt gemaakt van een draadelektrode, en zinkloodvonken, waarbij gebruik wordt gemaakt van een gevormde elektrode.
- Langzaam proces: EDM is relatief langzaam in vergelijking met andere bewerkingsmethoden, waardoor het het meest geschikt is voor kleine hoeveelheden en uiterst nauwkeurige klussen.
Toleranties en kwaliteitscontrole
Precisiebewerking vereist nauwgezette aandacht voor detail en een rigoureuze inzet voor kwaliteitscontrole om ervoor te zorgen dat onderdelen aan de gespecificeerde normen voldoen. In dit gedeelte onderzoeken we drie cruciale aspecten van kwaliteitscontrole bij precisiebewerking: geometrische dimensionering en toleranties (GD&T), statistische procescontrole (SPC) en kwaliteitsborging.A. Geometrische dimensionering en toleranties (GD&T)
Geometrische dimensionering en tolerantie, vaak afgekort als GD&T, is een systeem dat wordt gebruikt om de toegestane variaties in grootte, vorm, oriëntatie en locatie van kenmerken op een onderdeel te definiëren en te communiceren. GD&T is om de volgende redenen essentieel bij precisiebewerking:- Nauwkeurige communicatie: GD&T biedt een gestandaardiseerde taal voor ingenieurs, ontwerpers en machinisten om de ontwerpintentie en maatvereisten nauwkeurig te communiceren.
- Tolerantie verduidelijking: Het helpt bij het definiëren van de aanvaardbare variatie in kritische dimensies, en zorgt ervoor dat alle belanghebbenden de toegestane afwijkingen begrijpen.
- Verbeterde kwaliteit: GD&T bevordert een verbeterde kwaliteit door dubbelzinnigheid in ontwerpspecificaties te verminderen, waardoor het risico op fouten tijdens de bewerking wordt geminimaliseerd.
- Kost efficiëntie: Duidelijke GD&T-specificaties kunnen leiden tot lagere productiekosten, omdat de kans kleiner is dat onderdelen worden gesloopt of opnieuw moeten worden bewerkt als gevolg van misverstanden of verkeerde interpretaties.
- Complexe geometrie: Het is vooral handig voor onderdelen met complexe geometrieën, zodat alle onderdelen volgens de gewenste specificaties worden vervaardigd.
B. Statistische procescontrole (SPC)
Statistische Process Control (SPC) is een kwaliteitscontrolemethodologie die gebruik maakt van statistische technieken om het bewerkingsproces te bewaken en te controleren. SPC is om de volgende redenen essentieel bij precisiebewerking:- Process Monitoring: SPC helpt bewerkingsprocessen in realtime te bewaken en variaties of afwijkingen van de gewenste parameters te identificeren.
- Vroege detectie van problemen: Door het proces voortdurend te monitoren, maakt SPC de vroegtijdige detectie mogelijk van problemen die zouden kunnen leiden tot onderdelen die niet aan de specificaties voldoen, waardoor verspilling en herbewerking wordt verminderd.
- Gegevensgestuurde besluitvorming: SPC vertrouwt op gegevens en statistische analyses om weloverwogen beslissingen te nemen over procesaanpassingen, zodat het bewerkingsproces binnen aanvaardbare grenzen blijft.
- Verbeterde consistentie: SPC bevordert de procesconsistentie en vermindert de kans op het produceren van niet-conforme onderdelen.
- Minder uitval en herbewerking: Door procesvariaties snel te identificeren en aan te pakken, minimaliseert SPC de productie van defecte onderdelen, waardoor de afval- en herbewerkingskosten worden verlaagd.
C. Kwaliteitsborging bij precisiebewerking
Kwaliteitsborging bij precisiebewerking omvat een alomvattende aanpak om ervoor te zorgen dat vervaardigde onderdelen voldoen aan de gespecificeerde kwaliteitsnormen of deze zelfs overtreffen. Het omvat verschillende elementen, waaronder:- Procesdocumentatie: Gedetailleerde documentatie van bewerkingsprocessen, inclusief standaard operationele procedures (SOP's) en werkinstructies, zorgt ervoor dat elke stap consistent wordt uitgevoerd.
- Inspectie en meting: Rigoureuze inspectie en metingen met behulp van precisie-instrumenten en metrologische technieken verifiëren dat onderdelen voldoen aan gespecificeerde toleranties en kwaliteitsnormen.
- Ijking: Regelmatige kalibratie van bewerkingsapparatuur en meetinstrumenten is essentieel om de nauwkeurigheid en traceerbaarheid te behouden.
- Materiële verificatie: Verificatie van materiaaleigenschappen, samenstelling en kwaliteit is van cruciaal belang om ervoor te zorgen dat het gebruikte materiaal aan de ontwerpvereisten voldoet.
- Werknemerstraining: Programma's voor training en ontwikkeling van vaardigheden voor machinisten en kwaliteitscontrolepersoneel zorgen ervoor dat zij bekwaam zijn in hun rollen en verantwoordelijkheden.
- Root Cause Analysis: Wanneer niet-conforme onderdelen worden geïdentificeerd, wordt een analyse van de hoofdoorzaak uitgevoerd om de oorzaak van het probleem te achterhalen en corrigerende maatregelen te implementeren.
- CONTINUE VERBETERING: Een cultuur van voortdurende verbetering bevordert innovatie en stimuleert voortdurende verbeteringen in bewerkingsprocessen en kwaliteitscontroleprocedures.
- Klantenfeedback: Het verzamelen en analyseren van feedback van klanten helpt bij het identificeren van verbeterpunten en brengt bewerkingsprocessen in lijn met de verwachtingen van de klant.
Conclusie
A. De kunst en wetenschap van precisiebewerking
Precisiebewerking bevindt zich op het kruispunt van kunst en wetenschap, waar creativiteit, vaardigheid en innovatie samenkomen om onderdelen met hoge precisie te produceren die industrieën stimuleren en de moderne wereld vormgeven. Het is zowel een kunstvorm die het vakmanschap en de expertise vereist van machinisten die grondstoffen omzetten in kunstwerken van uitmuntende techniek, als een wetenschap die vertrouwt op de allernieuwste technologie, materiaalkunde en geavanceerde processen om ongeëvenaarde precisie te bereiken. De reis van precisiebewerking voert ons door het begrip van materialen en hun eigenschappen, de beheersing van snijgereedschappen en machines, en de nauwgezette controle van processen en toleranties. Het omvat de taal van geometrische dimensionering en tolerantie, de waakzaamheid van statistische procescontrole en de toewijding aan kwaliteitsborging. Precisiebewerking speelt een cruciale rol in diverse industrieën, van de lucht- en ruimtevaart en de automobielsector tot medische apparatuur en elektronica, en geeft vorm aan alles, van vliegtuigmotoren tot kunstmatige gewrichten en microchips. Het maakt de creatie mogelijk van componenten die met ongeëvenaarde nauwkeurigheid en betrouwbaarheid werken, waarbij vaak de grenzen van wat mogelijk is worden verlegd.B. Laatste gedachten
Nu we dit onderzoek naar precisiebewerking afsluiten, is het duidelijk dat dit vakgebied niet alleen over het maken van onderdelen gaat; het gaat om het creëren van mogelijkheden. De zoektocht naar precisie stimuleert innovatie en verlegt de grenzen van wat kan worden bereikt. Of het nu gaat om het delicate vakmanschap dat nodig is om de ingewikkelde tandwielen van een horloge te maken of om de geavanceerde technologie die nodig is om complexe luchtvaartcomponenten te vervaardigen, precisiebewerking vormt de kern van dit alles. De toekomst van precisiebewerking is veelbelovend. Vooruitgang op het gebied van materiaalkunde, automatisering en digitale technologieën blijft het landschap hervormen. Miniaturisatie, 3D-printen en duurzame productiepraktijken worden steeds prominenter, waardoor nieuwe horizonten voor de industrie worden geopend. In een wereld waar precisie belangrijker is dan ooit, blijft precisiebewerking een onmisbare pijler van de moderne techniek. Het is een bewijs van menselijk vernuft en ons onverzettelijke streven naar uitmuntendheid in elk facet van de productie. Naarmate de vraag naar hogere precisie en ingewikkeldere componenten groeit, zal precisiebewerking blijven evolueren, waarbij de uitdagingen van morgen worden aangegaan met dezelfde toewijding en precisie die deze al eeuwenlang kenmerken.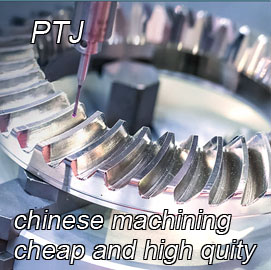
Onze Diensten
- 5-assige bewerking
- CNC frezen
- CNC draaien
- Bewerkingsindustrieën
- Bewerkingsproces
- Oppervlakte behandeling
- Metaalbewerking
- Kunststofbewerking
- Poedermetallurgievorm:
- Die Casting
- Onderdelengalerij
Casestudies
- Auto metalen onderdelen
- Machine onderdelen
- LED-koellichaam
- Bouwdelen
- Mobiele onderdelen
- Medische onderdelen
- Elektronische onderdelen
- Bewerking op maat
- Bicycle Parts
Lijst van materialen
- Aluminium bewerking
- Titanium bewerking
- Bewerking van roestvrij staal
- Koperbewerking
- Messing verspanen
- Bewerking van superlegeringen
- Peek-bewerking
- UHMW-bewerking
- Unilate Bewerking
- PA6 Bewerking
- PPS-bewerking:
- Teflon-bewerking:
- Inconel-bewerking:
- Bewerking van gereedschapsstaal
- Meer materiaal
Onderdelengalerij